Useful Insights On Stock Obsolescence and MRO Spares Management
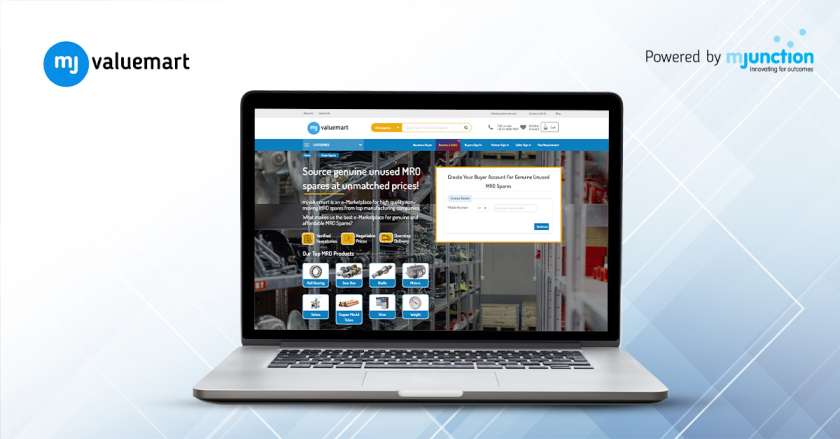
Stock obsolescence occurs when a company has an excess inventory of old or outdated products, particularly maintenance, repair, and operations (MRO) spare parts, that are no longer needed or wanted. Stock obsolescence can lead to increased storage costs and reduced profitability. If you are looking for information on stock obsolescence and MRO spare management, here is a useful read. As one of the leading e-marketplaces for unused and genuine MRO spares, we share with you some useful insights:
1. Factors behind stock obsolescence: It can occur due to different factors such as:
- Equipment upgrades
- Product discontinuation
- Changes in technology
- Changes in regulations
- Changes in customer demands
2. Stock obsolescence can lead to excess stock: When an MRO part is no longer being manufactured by the original manufacturer, it can result in excess inventory and increased maintenance costs for companies that continue to use these parts. It can tie up a significant amount of valuable capital and result in unnecessary expenses.
3. Stock obsolescence can result in stockouts: Obsolescence can also lead to stockouts, where a company runs out of a particular MRO spare part due to its unavailability in the market. This situation can cause downtime and result in significant maintenance expenses. Moreover, stockouts can have a negative impact on a company's profitability.
4. Managing stock obsolescence: Stock obsolescence can be effectively managed by following these steps:
- Regular inventory assessment: This is done to ensure that sufficient stock levels are maintained. With an effective inventory assessment programming place, obsolete critical MRO spares can be easily identified and segregated from the rest of the inventory.
- Collaboration with suppliers: When companies partner and collaborate with suppliers, they can improve their MRO spare parts management. By establishing strong relationships with suppliers, a company can stay up-to-date on product and spare parts developments and any potential discontinuations. This can help prevent stockouts and excess inventory.
- Implementing an effective MRO spares parts management system: Implementing a robust spare management system can help manage stock obsolescence. By conducting regular assessments of inventory, a company can identify obsolete products and take necessary actions to prevent excess stock situations. Also, by analysing usage patterns companies can gain valuable insights into which spare parts are frequently used and which are not.
- Proper documentation: Maintaining proper documentation of equipment and MRO spares is critical for effective management of obsolescence. By tracking purchase dates, usage patterns and other relevant information, a company can identify outdated products more easily as well as take steps to mitigate the risks involved. Documentation is also important for meeting compliance and regulatory requirements. Many industries require companies to keep detailed records of equipment and spare parts for compliance purposes
- Liquidating the inventory: Liquidating inventory involves selling excess stock through clearance sales and auctions. This strategy helps generate revenue while freeing up valuable storage space. Liquidation also prevents the stock from becoming obsolete and losing value over time. By selling off the items quickly, a business can recoup some of its original investment—and use those funds to purchase new parts.