Importance of proper maintenance of welding machines
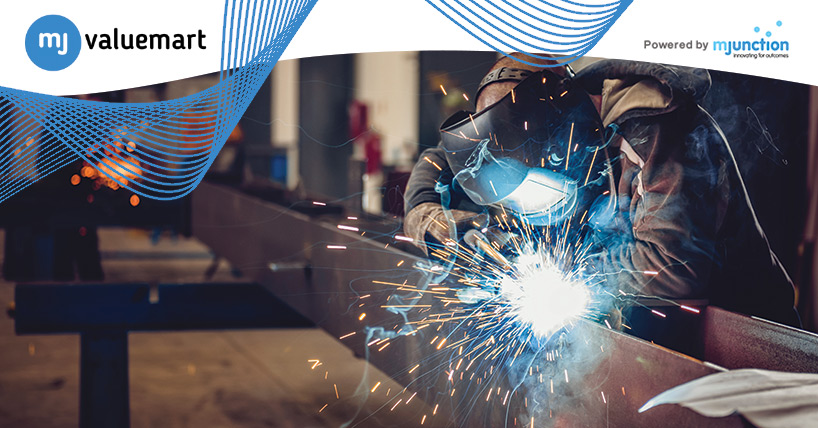
A welding machine, also known as a welder, plays an important role in metalworking. This powerful tool utilises thermal energy to fuse or separate metal components by melting them. With its ability to generate intense heat, a welding machine serves as a valuable asset for professionals in the welding industry. It enables the transformation of metal, giving it new shapes or facilitating the joining of different metals together. Whether it's for fabrication, repairs, or creative metalwork, a welding machine proves indispensable in achieving precise and robust metal connections. However, to ensure that welding machines perform at their best and deliver reliable results, regular and proper maintenance is essential.
Proper maintenance also extends the lifespan of the equipment, avoiding costly repairs or premature replacements. By conducting regular maintenance tasks, such as cleaning, inspecting, and lubricating the equipment, you can identify and address minor issues before they escalate into major problems. This proactive approach helps preserve the integrity of the machine's components, ensuring they function efficiently and effectively over an extended period.
By giving due attention to the maintenance and functionality of your welding machine, you can minimise its downtime. A malfunctioning machine can halt production until the problem is resolved. This unplanned interruption can lead to significant bottlenecks and compromised quality, especially when it occurs unexpectedly.
Also, it enhances safety by identifying and addressing potential hazards. Regular inspections and upkeep allow for the early detection of safety risks, such as faulty wiring, loose connections, worn-out protective components, or inadequate ventilation. By promptly addressing these issues, you can mitigate the potential for accidents, electrical shocks, fires, or other workplace hazards.
It also saves costs by preventing major breakdowns and reducing energy consumption. A machine breakdown can have costly consequences. It can disrupt schedules, leading to reduced efficiency on the production floor and potentially less work for your employees. Beyond the loss of time and productivity, a broken machine can result in unexpected expenses and high repair or replacement costs.
Signs such as excessive heat or wire feed issues may indicate problems with the equipment. Some of these issues can be resolved through simple measures while others may require more complex repairs to internal components. However, with proper maintenance and proactive care, many of these problems can be identified and addressed early on. If you are looking for information on proper maintenance of welding machine parts, here are some tips:
1. Selecting the right welding equipment is important for proper maintenance. Consider factors such as the usage conditions, metal types, and amperage requirements when selecting a welding machine.
2. To ensure optimal performance and longevity of a welding machine, it is important to adhere to its specified guidelines.
3. Check the user manual or contact the manufacturer for advice on how often to perform maintenance and the proper procedures to follow. They can offer helpful tips on how to take good care of your particular model.
4. Regularly replace consumable parts, such as tips or nozzles on welding torches. Over time, these components can wear out or become damaged, leading to diminished performance and potential defects in the weld.
5. To maintain optimal operation and prevent operational disruptions such as flashovers or burning, it is important to ensure the earth electrode of the machine is intact, clean, and free from cracks. An uneven or damaged earth electrode can lead to power loss and result in inferior welding outcomes.
6. To ensure the longevity and optimal performance of welding equipment, it is essential to keep the material, equipment, and the surrounding area clean. The presence of dirt, dust, or debris on the material, electrode, or welding table can lead to circuit flashes, posing a risk of damaging both the material being welded and the equipment itself.
7. Regularly check all cables to ensure they are not loose, worn out, or damaged in any way. Cables can get damaged when people step on them frequently, wrap them improperly around objects, or store them carelessly. If you notice any damage to a cable, replace it immediately with a new one. It's important to give the same attention to ground leads, as they can also suffer similar wear and tear over time. By replacing worn or broken ground leads, you will maintain a reliable welding machine and ensure a safe working environment.
8. Properly store your welding machine parts to maintain functionality and extend their lifespan. When storing welding rods, always keep them upright to prevent damage that could compromise the quality and safety of your work. Store the rods in waterproof containers, ensuring that different types are kept separate to maintain their dryness and prevent mixing. For hoses, loosely coil them to prevent long-term damage and remove any kinks or knots.
Looking for genuine and quality-tested welding machine spare parts in India?
Explore genuine and unused spare parts at mjvaluemart - India’s most trusted e-marketplace for non-moving MRO spares. Negotiate directly with the seller and get attractive prices from verified inventories.